Owing to the boom in the use of artificial grass in landscaping-gardening, for some years now, our industry has been seriously affected by unqualified operators. In addition to this, a large number of websites dedicated to the sale and installation of artificial grass has suddenly appeared. Unfortunately, it is common that those who are behind these websites lack experience, professionalism, reliability and transparency. Regrettably, the information they publish is far from the truth or is directly false or misleading, which leads to the consequent distrust of the buyer
The information related to certain terms such as guarantees, or other characteristics such as the resistance of the material to static electricity or fire is liable to be manipulated and subsequently used as a marketing or customer acquisition tool
We will now fill you in on the truth, the whole truth and nothing but the truth about artificial grass and at the same time we will challenge falsehoods and reveal some ploys that are used
The information related to certain terms such as guarantees, or other characteristics such as the resistance of the material to static electricity or fire is liable to be manipulated and subsequently used as a marketing or customer acquisition tool
We will now fill you in on the truth, the whole truth and nothing but the truth about artificial grass and at the same time we will challenge falsehoods and reveal some ploys that are used
Warranty
Guarantees of 9, 10 and 12 years ... or even more! ... There is much hot air regarding the guarantees behind artificial grass, and there is little truth in these high figures and ostentatious logos ...
We will banish the myths and urban legends, and clarify which guarantees are actually associated with artificial grass. The guarantee that goes along with the purchase of any artificial grass in gardening-landscaping focuses on two issues:
- Firstly, the coverage due to flaws in production, which can be seen after unpacking the material, such as:
- Obvious production flaws
- Damage to the product
- Stitching of different colours, because the base curl has been woven at a greater height than the other seams
- Yarn that is higher in some parts than in others
- Other defects derived from the production of the yarn that makes up the artificial grass
- The second coverage, which we will call “long term”, guarantees the stability of the yarn when exposed to UV rays. This means that the grass will not turn white or blue during the stated period. Here we come to the numbers war which some companies resort to in order to catch the attention of potential customers, by offering increasingly high guarantee periods, which, however, are totally false ... We will now reveal the truth of the matter
The question could be left at that and anyone advertising a guarantee longer than 9 years should need to explain how it is possible to claim longer guarantee periods than those stated by the fiber manufacturers themselves... However if we look even further we find that the intensity of UV rays that the artificial grass may have to endure in Spain, is not the same as it would be in Holland, or in Egypt. For this reason, a filter is applied according to the degree of intensity of solar radiation ( expressed in watts / m2 ) that the artificial grass can endure once installed
In order to determine this, we will use the following world map, in which areas of the planet are indicated according to the level of radiation. In the case of Spain, the maximum applicable degree is up to 200 W / m2 for the center and south of the Iberian Peninsula
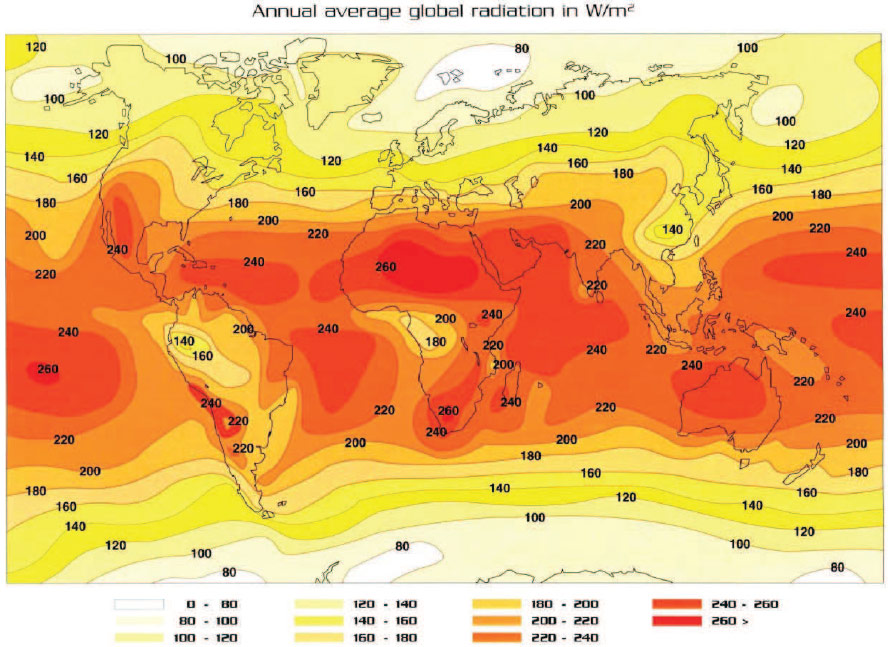
According to this, we must subtract one year from the standard term stated by the manufacturer of any artificial grass that is to be installed in Spain. This means that the maximum warranty period applicable to Spain for decorative artificial grass should in no case be greater than 8 years ( 9 as a maximum period, minus 1 for Spain, due to the high level of solar radiation )
We must pay special attention to those suppliers who extend the maximum guarantee period to their entire range of models, from the most basic and cheapest to the most expensive and of highest quality, mainly because this defies logic, as shorter guarantee periods are granted for basic yarn, and more advanced and complex yarn benefits from longer guarantee periods
No manufacturer of artificial grass in the world applies the same guarantee period to all the models that make up its range. SUMIGRAN’s range offers real guarantee periods applicable to Spain, ranging from 5 to 8 years
The latest developments by manufacturers of artificial grass yarn should be able to guarantee UV resistance of up to 10 years for areas with a radiation level of 200 W / m2. However, here we are talking about yarn that is in the process of development and has not yet been commercialized
We consider it of utmost importance to clarify this, in other words: do not get carried away by very attractive guarantee periods that from a commercial point of view are not real at all. Avoid unpleasant surprises, and understand that no manufacturer would honour potential claims that fall outside the guarantee period
Dimensional stability
Due to the manufacturing process and the nature of the raw materials used, artificial grass is a product subject to possible contraction or expansion
The difference between maximum and minimum temperatures ( thermal amplitude ) to which the artificial grass will be exposed over a period of time, will subject the material to "stress", the consequence of which could be dimensional variation ( contraction or expansion )
We are referring to an inherent reaction of the product, like that of any material exposed to weather conditions, which will occur in extreme circumstances, such as at high peaks of temperature during the day with a notable drop in temperature at night. This could be exacerbated if the grass has been installed on a concrete or ceramic floor ( which generate more heat than installation on natural terrain )
If we use silica sand as ballast on the area, it can give greater dimensional stability to artificial grass, as in this way, the weight which is put on the product will offer greater resistance to the possible contraction or expansion of the backing
Some international organizations linked to the artificial grass market recognize as acceptable a dimensional stability, in which contraction or expansion is equal to or less than 1%
Shrinkage
For years, the incorporation and use of polyethylene ( PE ) fibres in the production of artificial grass was a notable improvement in terms of the smoothness that could be achieved by use of this polymer. However, it is also true that the critical point of heat resistance is lower than that of other materials ( such as polypropylene which is usually used for the backing / root of artificial grass )
Polyethylene can remain stable up to a temperature close to 75 ° C. From this temperature upwards, the material becomes much more sensitive and unstable, and the fibers begin to experience gradual and increasing shrinkage. This contraction is irreversible, causing a deformity in the affected fibres
The following table shows a reference of 75ºC as being the critical point for polyethylene, and how from that point on an obvious increase in the shrinkage ratio of the fibers occurs
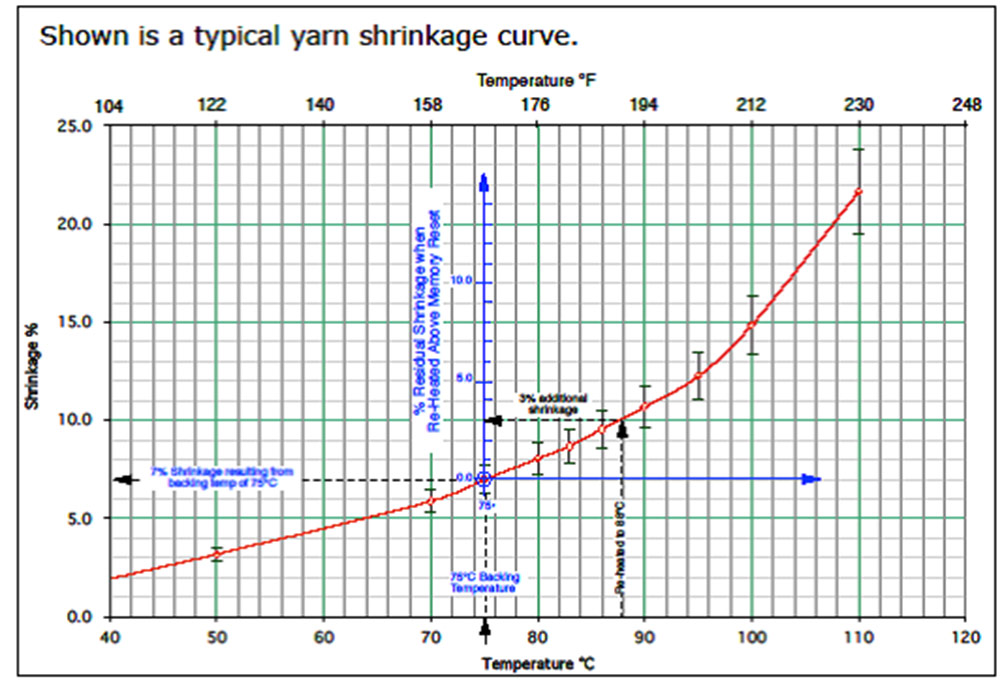
For example, in the case of grass installed in a garden or terrace facing south and exposed to the sun during the hours of highest heat intensity ( from noon to 5 p.m. ) special care is needed if the grass is installed next to walls or vertical surfaces which are especially reflective ( e.g. windows, glass doors, smooth white walls, tiles, metal plates or any similar material that can reflect light ), as these can act as a "mirror", reflecting the solar radiation they receive onto the nearest grass, which will receive double radiation ( direct radiation and reflected radiation ), which means that the temperature would be in excess of the critical point of resistance of polyethylene, causing a band of +/- 15-30 cm of damaged material next to the reflective surface
These are our recommendations ( specifically for professional fitters ):
- Examine the area carefully, paying special attention to any possible reflection or reflective surfaces that may cause concentration of the sun's rays on the area
- Ensure that the user is fully informed about artificial grass and its characteristics, and especially the fact that it can be damaged by exposure to temperatures in excess of 75ºC
- Sand ballast helps to distribute and absorb the heat
Static electricity
Due to its own composition and structure, artificial grass cannot be a permanent antistatic product
Over the last few seasons, certain companies have highlighted that they have some antistatic models ( some even dare to extend that quality to their entire range... ). We recommend asking for the test certificate, supplied by an independent accredited laboratory regarding the resistance test to static electricity and conductivity, of the model or models that are advertised as "antistatic", something that they will more than likely be unable to show ...
As mentioned earlier, artificial grass and antistatic grass are almost mutually incompatible terms. However, for the last few years, with the evolution in the treatment of polymers and the process of yarn extrusion, additives can be incorporated into them which will reduce the accumulation of static charge, but which will in no case eliminate it completely and permanently, especially as the materials that make up the back on which the yarn is woven could not have undergone the same treatment process as the yarn itself
Static electricity is produced when electrical charges accumulate on the surface of a nonconductive object, normally occurring due to the friction between two materials. In the case of artificial grass, playing on it ( rubbing ) can cause an accumulation of a triboelectric charge. Moreover, dry and cold conditions increase static electricity. This is specific to the physical characteristics of the yarn used to manufacture the artificial grass, and it is not a defect of the yarn
The phenomenon occurs more frequently on newly fitted surfaces, and the frequency and intensity of it tends to diminish with the passage of time
The accumulation of static charge can be alleviated by keeping the artificial grass moist. Furthermore, in order to increase the accumulation of moisture in the artificial grass, we can use silica sand as ballast to increase moisture retention and to reduce evaporation
Furthermore, artificial grass may be cleaned using certain chemical products. Specific products with antistatic properties exist, however, given that these products are not easy to obtain, we have a more home-made option, namely to sprinkle the artificial grass with a softener ( similar to the type we use to wash clothes in a washing machine ) diluted in water
Whereas, for the time being, the results of antistatic treatment on artificial grass yarns are not as satisfactory as we would like, we recommend applying the palliative measures as previously described in cases where it is necessary
Fire resistance
In discussing the relationship of artificial grass with fire and its resistance to it, we must start by recognizing the fact that the product in question is designed for use in outdoor areas. It is not a carpet designed to be fitted inside buildings, where the Technical Building Code stipulates which characteristics must be complied with in terms of fire resistance
Not being a product subject to regulations regarding fire resistance, as it is an outdoor carpet, most manufacturers do not subject their products to fire resistance tests according to any of the international or continental standards. However, with the increasing popularity of artificial grass as a covering with multiple uses, fire resistance tests have been initiated, most of them in accordance with EN 13501-1
Due to the type of fibre and backing used and the coating and the structure of artificial grass as a whole it is popularly classified as "self-extinguishing", a classification which is reinforced if silica sand gravel is also used
Even allowing for these characteristics, it is advisable to take certain minimum precautions regarding possible sources of heat to avoid deterioration to the fiber
If artificial grass with a specific type of fire classification conforming to the CTE is required, we recommend informing your supplier of this requirement and requesting the appropriate fire resistance certificate in advance of purchaseIf artificial grass with a specific type of fire classification conforming to the CTE is required, we recommend informing your supplier of this requirement and requesting the appropriate fire resistance certificate in advance of purchase
Pets and "antimicrobial" artificial grass
Artificial grass has always been considered pet-friendly as it is durable and non-abrasive
The latest "trend" in the market is for certain companies to advertise their artificial grass as having “antibacterial” properties. However, this strategy implies that it protects against animal excrement, which appears to be an attempt to instil an unfounded fear and distrust in clients towards models that are "not antibacterial "
As in the case of antistatic artificial grass, an antibacterial quality can be added to the fibre by applying additives that act as inhibitors to the development and growth of bacteria during the extrusion process. The fact is that this treatment is not permanent anyway, although this point is never mentioned for obvious reasons
In any case, clients who have an interest in antibacterial artificial grass should always ask the company beforehand to supply documents issued by an independent laboratory which certify that the model advertised is in fact antibacterial. It is essential to also ask how long this antibacterial property will last
It is common to see how some companies extend to their entire range of artificial grass a quality that could only possibly apply to one or two models i.e. those which have been treated with antibacterial additives. It is especially remarkable as yarn that has undergone this treatment is quite scarce in today’s market as it is not very popular due to low demand
The care and cleaning of a garden that will also be enjoyed by our pets relies mainly on common sense. The dirt that our pet may have caused should be removed as soon as possible using water and detergent, just as if it had happened inside the house
If we want to clean our garden more regularly, we can occasionally use a special antibacterial cleaner or disinfectant for these types of surfaces, and simply follow the instructions stated by the manufacturer
Dictionary of technical terms ( gauge, DTEX, stitches, etc... )
Gauge: this is the distance in separation between any seam line and the adjoining one on the backing on which the fibres are woven. It is expressed in inches ( one inch equals approximately 2.54 cm ). The most common gauges are 3/8 ", 5/8", 5/16 ", 5/32" and 3/16 ". Obviously, this value has a decisive influence on the fibre density per m2 of each model: the smaller the distance between needles, the greater the density of the manufactured product
Decitex ( Dtex ): this is a very popular unit of measurement in the textile industry. It indicates the mass of the fibre used ( in grams ) per 10,000 linear metres. To a certain extent, it refers to the consistency and calibre of the filaments that make up the fibre of the artificial grass
A higher Dtex does not mean a better product. This will be explained using the three cases outlined below. Although all of them have the same Dtex value, very different results are finally obtained
- Model A: artificial grass with a fibre of 15000 Dtex, composed of 2 yarns with 8 filaments per strand, for which the green-coloured monofilament will be of a fairly thick calibre, even being a little coarse for an artificial garden lawn
- Model B: artificial grass with a fibre of 15000 Dtex, composed of a combination of 12 green-coloured filaments plus 8 strands of curled yarn on the backing, which distributes the weight of the fibre onto more filaments, which are of lower calibre. This gives the product a more natural appearance and feel
- Model C: artificial grass with a fibre of 15000 Dtex, composed of 3 different types of yarn in a combination of 8 filaments of one type, plus 6 of another type, plus 8 filaments of curly root yarn. This configuration, which is even more complex than model B, is more natural as the final product because the yarn recovers ( its vertical position after being stepped on ) in a different way, and creates different textures, similar to natural grass
In addition to this, the fibre of the artificial grass can be composed of a single yarn, or a combination of two yarns ( the most common in garden grass ), or even the combination of up to 3, or even 4 different yarns ( only for the most exclusive products ). Also keep in mind that the fibre can be made up of two or three yarns with a different number of filaments
Fibre height: this indicates the height of the yarn in millimetres and is a factor that affects the final weight of the fibre used ( quantitative factor ). Obviously, for taller yarns there is more fibre consumption ( more fibre weight ), which results in the final product being softer and more comfortable
Stitches every 10 cm: this indicates the number of seam stitches that have been woven every 10 cm, on a seam line. This factor will affect the total product density ( stitches per m2 ), along with the gauge. Like fibre height, it is a quantitative factor which will determine the fibre weight of the final product
Density ( stitches per m2 ): the combination of the gauge and the number of stitches on the seam line determines what the total density of the grass will be, which is usually expressed in the number of stitches per m2
The density is a quantitative calculation factor and does not in itself determine the final quality of the product. In any case, it contributes in determining the fibre weight of each model, which affects its texture
Logically, with the same quality and height of yarn, artificial grass of higher density is better than one of lesser density. However, this statement has its exceptions because excess stitching can result in the final product being coarse, of unpleasant texture and ultimately not very suitable for gardening and landscaping. A balance between yarn quality and density should always be sought
Yarn structure: this is one of the basic characteristics of artificial grass fibres. There are 2 main types: monofilament yarn and fibrillated yarn. Monofilament yarn consists of a single continuous filament, which can be straight or textured ( curled ), while fibrillated yarn is a band ( much thicker than monofilament yarn ) of pre-cut length, creating small filaments from the yarn. In the case of monofilament yarn there are several yarns per stitch, while in fibrillated yarn it is a single yarn per stitch
In relation to this, the recent appearance of new "micro monofilament" yarn ( MMF ) should be mentioned, as this has been one of the greatest technical advances in the manufacturing process of artificial grass. These are fibres with the structure of monofilament yarn, but have been greatly improved and are now able to be extruded in finer calibres ( smaller width and thickness ). This difference gives it more softness and a more pleasant texture
Even though it is yarn of a smaller calibre, that is with less consistency, thanks to advances in the quality of the polymer and its extrusion system, special form can be given to its shape, which favours recovery ( from the vertical position after being stepped on ). Also, being thinner yarn, we can reach very high densities, which provide more bounce ( by multiplying the curled root fibres ) and elasticity to the product as a whole
Yarn composition: this is another of the main characteristics of the fibre for artificial grass. It refers to the origin-raw material of the polymer derived from the oil used in the manufacture of the product. The materials used for the manufacture of artificial grass fibres are polyethylene, polypropylene and polyamide
Yarn thickness: this indicates the thickness of the yarn in microns, a characteristic that is linked to the Dtex of the fibre
Yarn width: this indicates the width of the yarn in millimetres, a characteristic which just like the thickness, is linked to the Dtex of the fibre
Shapes of the yarn cross-section:
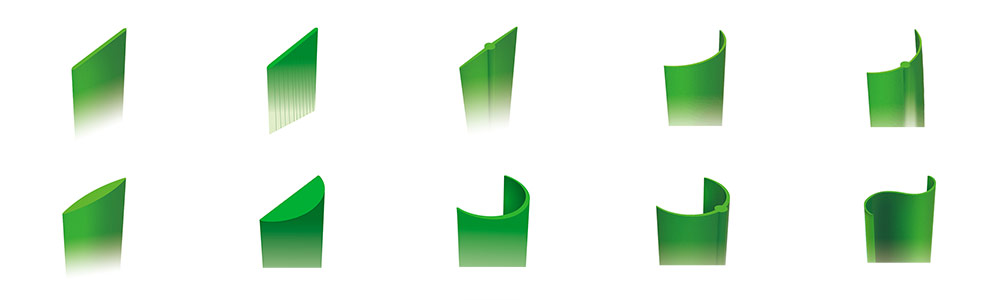
Micro monofilaments ( MMF )
Micro monofilaments. When less is more
What are micro monofilaments ( MMF ) ? Until now, it was necessary to use yarn of a certain thickness and calibre to be able to extrude a special shape in such a way that it could favour the recovery of a vertical position after being stepped on while maintaining both the production process and keeping the material free from problems
In order to make soft fibres which were more pleasant to the touch, the only possibility used to be flat yarn ( flat tape ), but this type of yarn has disadvantages compared to specially shaped yarn ( yarn shaped in "V","C","U","W","S” forms and many other options that have been introduced onto the market over the years ), which is their reduced recovery ( verticality ) after being stepped on
In order to be able to manufacture yarn of a special shape, it was necessary to resort to fibres of a greater mass. This ensured a better recovery, but it simultaneously hardened the fibres significantly, making them more rigid and rougher to the touch. Consequently, it was less suitable for installation in gardens that were subjected to intense use or on those whose use was for sitting, lying, or walking barefoot on
The technical advances in polymers for the production of polyethylene fibres, as well as in the extrusion heads used in the extrusion process, mean that the structure of the classic monofilaments used in the manufacture of artificial grass has considerably evolved over recent years
Over the last year, Micro monofilaments ( MMF ) have been developed and in SUMIGRAN, we have decided to use them for practically all of our range. What do they consist of ? Starting from more advanced polymers and new extrusion systems, they allow us to give special forms to the shape of the yarn ( forms that were previously only possible for yarn of greater mass ). By combining low mass yarns with the possibility of working with special shapes we combine in a single filament the virtues of low calibre yarns ( softness, pleasant touch ) with the virtues of yarns with special shapes ( recovery after being stepped on, resistance to use )
In addition, being ( yarn ) of smaller calibre, it offers a more natural visual appearance and allows us to make artificial grass in very high densities
If higher calibre yarn were used, there was a point of saturation in the process of weaving the fibres, where high densities could not be reached or, in the case of being able to reach them, products were created that were very rough visually and to the touch. By using MMF we can achieve much higher densities with a much more natural visual appearance
Taking into account that the main progress achieved through the use of MMF has occurred in straight yarns ( the green fibres that make up artificial grass ) and not so much in curly yarn, by increasing the density a much softer and more elastic feeling of the resulting product is achieved, because the amount of curly fibre is substantially multiplied compared to a similar model ( in fibre weight ) manufactured using classic monofilaments, which is what makes grass springy
In short, the use of MMF allows us to work with more efficient fibres. Fibres of less weight, but produced with the correct shape with a suitable combination of yarn height / density which allows us to create products that easily meet the objectives of all artificial grass: a natural appearance, softness, recovery after being stepped on and comfort
Manufacturing process
Extrusion of the yarn
The granules of the selected polymer, which will be the main raw material from which the yarn is to be manufactured, are mixed with the different additives that will give it certain qualities or properties, such as its colour, resistance to UV rays, touch-texture, or the ability to reduce unnatural brightness
Once made, the mixture is heated and pressed, forcing it to pass through a hole made in the extrusion head, which will give form to the shape of the yarn ( from the classic "flat tape", through "concaves in C or U" forms, and more rigid shapes such as the "W" shape, or the "lobed in triple C", to the "diamond" shape or "central nerve", etc... )
When leaving the extrusion head it falls directly into a tank of water that lowers its temperature and thus it solidifies and a process of applying tension to the yarn starts, subjecting it to different forces of traction, and braiding, to acquire greater strength. Finally, the yarn is wound into rolls
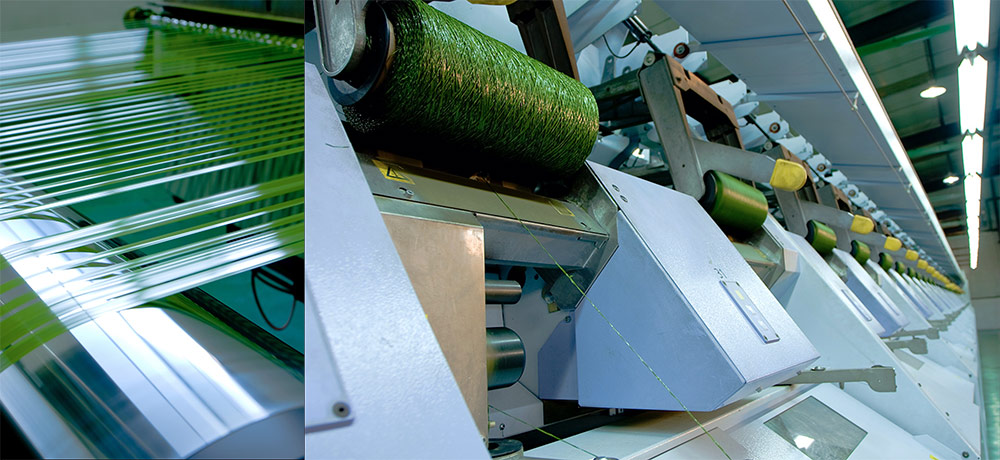
Tufting
Tufting machines operate according to a principle similar to that of sewing machines. By means of needles, the yarn is fixed to a prefabricated support backing in 4-meter-wide roll format ( usually made of polypropylene, which can be of different types, in order to give more grip to the fibres and greater dimensional stability to the final product, making it flexible enough ), creating stitches
In this process, the physical characteristics that the artificial grass will assume are configured. Its density will be determined ( according to the gauge and linear stitches that will be used ) and the height of the fibre
During the process, the operators of the machine visually check that it is being carried out properly; they can make small corrections to the material while production is in progress, or if it is necessary, they can halt the process of "tufting" stopping the machine in the case where a correction is required
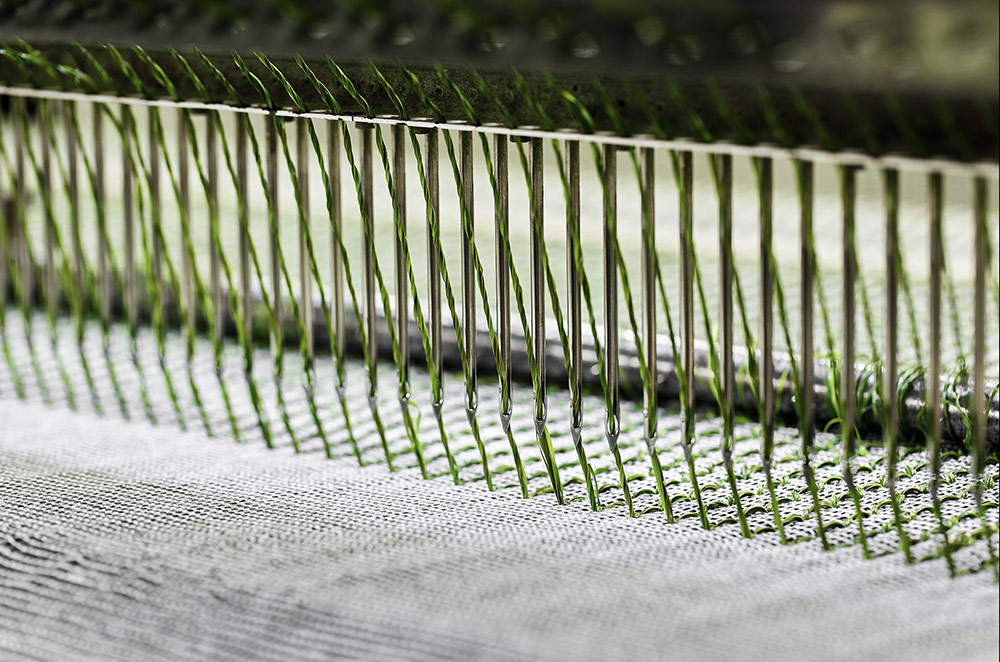
Coating
After weaving or "tufting", the fibres are not completely fixed to the backing support on which they have been woven, and if they are tugged they can be pulled out. That is why they must be fixed to the backing. For this, a liquid adhesive is applied to the backing, putting the product through baths containing the adhesive, or by other application techniques, such as mobile brushes
Next, the product is passed through a linear oven that performs the function of "curing" ( drying ) the adhesive, which then solidifies, thus fixing the loops of the sewn yarn ( stitches ) to the primary backing
After curing in the oven, perforation is carried out ( which consists of making small holes of +/- 0.5 cm in diameter at a ratio of +/- 60-80 holes/m2 depending on the model ) to allow water drainage which is essential if the artificial grass is going to be installed on natural ground
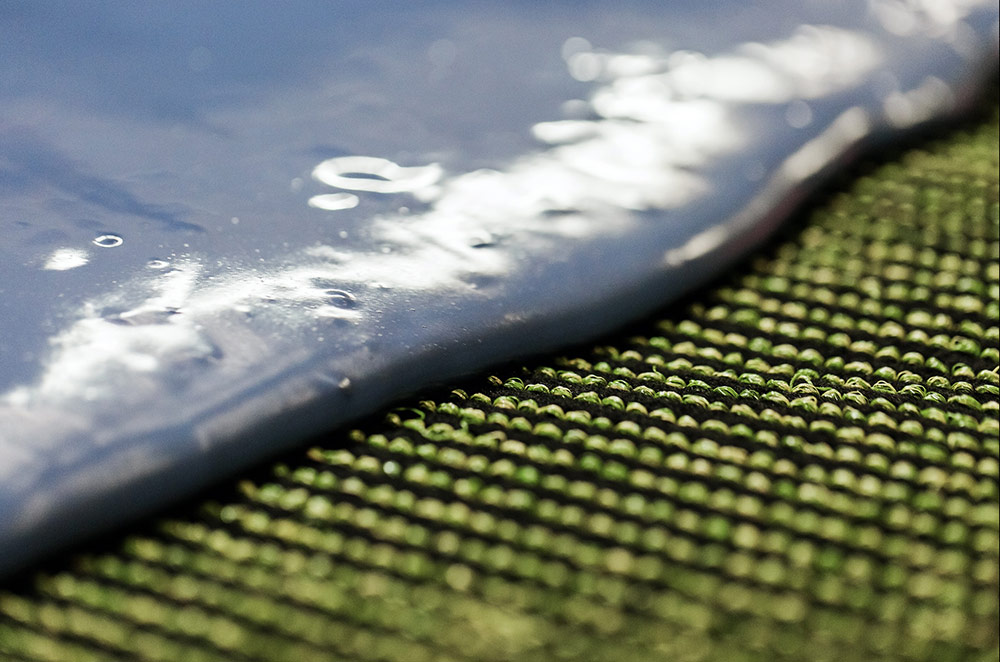
Quality control, winding and packing
Finally, we carry out visual quality control. After this check, the material is rolled into rolls that are then wrapped with protective plastic
Finally, the product is ready for distribution